What is a Bill of Materials (BOM) and Why It’s Crucial for E-Commerce Inventory Management
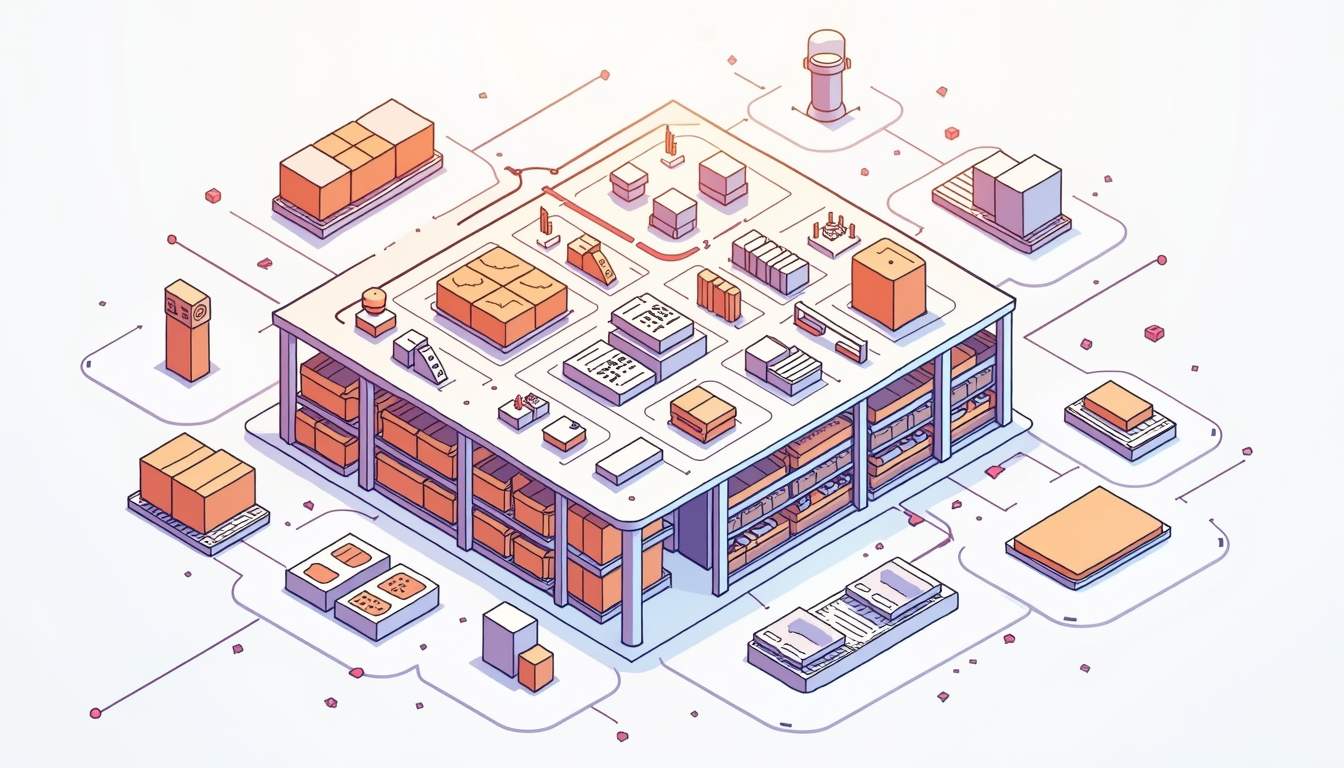
In the dynamic world of e-commerce, efficient inventory management is a cornerstone of success. One of the key tools that businesses utilize to streamline their inventory processes is the Bill of Materials (BOM). Understanding what a BOM is and how it integrates into e-commerce operations can significantly enhance the efficiency and profitability of a business. This comprehensive guide explores the concept of a BOM, its importance, and how it can be leveraged for optimal inventory management.
Understanding the Bill of Materials (BOM)
Definition and Components of a BOM
A Bill of Materials (BOM) is a comprehensive list of raw materials, components, and instructions required to construct, manufacture, or repair a product or service. It serves as a blueprint for product creation, detailing every item and process involved. A typical BOM includes item names, part numbers, descriptions, quantities, units of measure, and procurement sources.
The BOM is often visualized as a hierarchical representation, starting with the finished product at the top and breaking down into sub-assemblies and individual components. This structure helps in understanding the relationships and dependencies between different parts of a product, ensuring that nothing is overlooked during production.
In e-commerce, BOMs are not just limited to physical products. They can also apply to digital products and services, where the list might include software components, licenses, and digital assets necessary for delivery.
Types of BOMs
There are several types of BOMs, each serving different purposes depending on the industry and product complexity. The most common types include Engineering BOMs (EBOM), Manufacturing BOMs (MBOM), and Sales BOMs (SBOM). An EBOM is developed during the product design phase and includes all the technical specifications. An MBOM is used during the manufacturing process and includes additional details like packaging materials and assembly instructions. An SBOM is used for sales and customer service purposes, focusing on the final product configuration.
Choosing the right type of BOM is crucial for ensuring that all departments involved in the product lifecycle have the information they need. This ensures seamless communication and coordination across design, production, and sales teams.
For e-commerce businesses, the choice of BOM type can impact how efficiently they manage their inventory and fulfill customer orders. A well-structured BOM can help in predicting material requirements, managing suppliers, and reducing lead times.
The Importance of BOM in E-Commerce Inventory Management
Streamlining Inventory Processes
A BOM plays a pivotal role in streamlining inventory management processes. By providing a detailed list of all components required for a product, it helps businesses maintain optimal inventory levels. This prevents overstocking and understocking, both of which can have significant financial implications.
With a BOM, e-commerce businesses can automate reordering processes, ensuring that materials are replenished just in time for production. This reduces the need for large inventory holdings, freeing up capital and storage space. Additionally, it minimizes the risk of production delays due to missing components, thereby enhancing customer satisfaction.
Moreover, BOMs facilitate accurate forecasting and demand planning. By analyzing historical data and trends, businesses can predict future material requirements and adjust their inventory strategies accordingly. This proactive approach helps in maintaining a competitive edge in the fast-paced e-commerce market.
Enhancing Product Quality and Consistency
Consistency in product quality is a critical factor for success in e-commerce. A BOM ensures that every product is manufactured according to the same specifications, reducing the likelihood of errors and defects. This consistency builds customer trust and loyalty, leading to repeat business and positive reviews.
By standardizing the production process, a BOM also simplifies quality control and compliance checks. It provides a clear reference for identifying deviations from the standard, enabling quick corrective actions. This not only enhances product quality but also reduces waste and rework costs.
Furthermore, a BOM can be used to track changes and updates to product designs. This ensures that all stakeholders are aware of the latest specifications, preventing miscommunication and errors during production. Keeping a detailed history of changes also aids in troubleshooting and continuous improvement efforts.
Facilitating Efficient Supply Chain Management
Effective supply chain management is crucial for e-commerce businesses to meet customer expectations and stay competitive. A BOM provides valuable insights into the supply chain, helping businesses identify key suppliers and manage relationships effectively. By understanding the dependencies between different components, businesses can negotiate better terms and ensure timely deliveries.
Additionally, a BOM aids in risk management by identifying potential supply chain disruptions. By analyzing the BOM, businesses can develop contingency plans and alternative sourcing strategies to mitigate risks. This ensures continuity of operations and minimizes the impact of unforeseen events.
Furthermore, a BOM can be integrated with other supply chain management tools, such as Enterprise Resource Planning (ERP) systems, to enhance visibility and coordination across the supply chain. This integration enables real-time tracking of inventory levels, order statuses, and supplier performance, facilitating informed decision-making and strategic planning.
Implementing a BOM in E-Commerce Operations
Steps to Create an Effective BOM
Creating an effective BOM requires careful planning and attention to detail. The first step is to define the scope and purpose of the BOM, considering the specific needs of the business and the product. This involves identifying all components and materials required for the product, along with their specifications and sources.
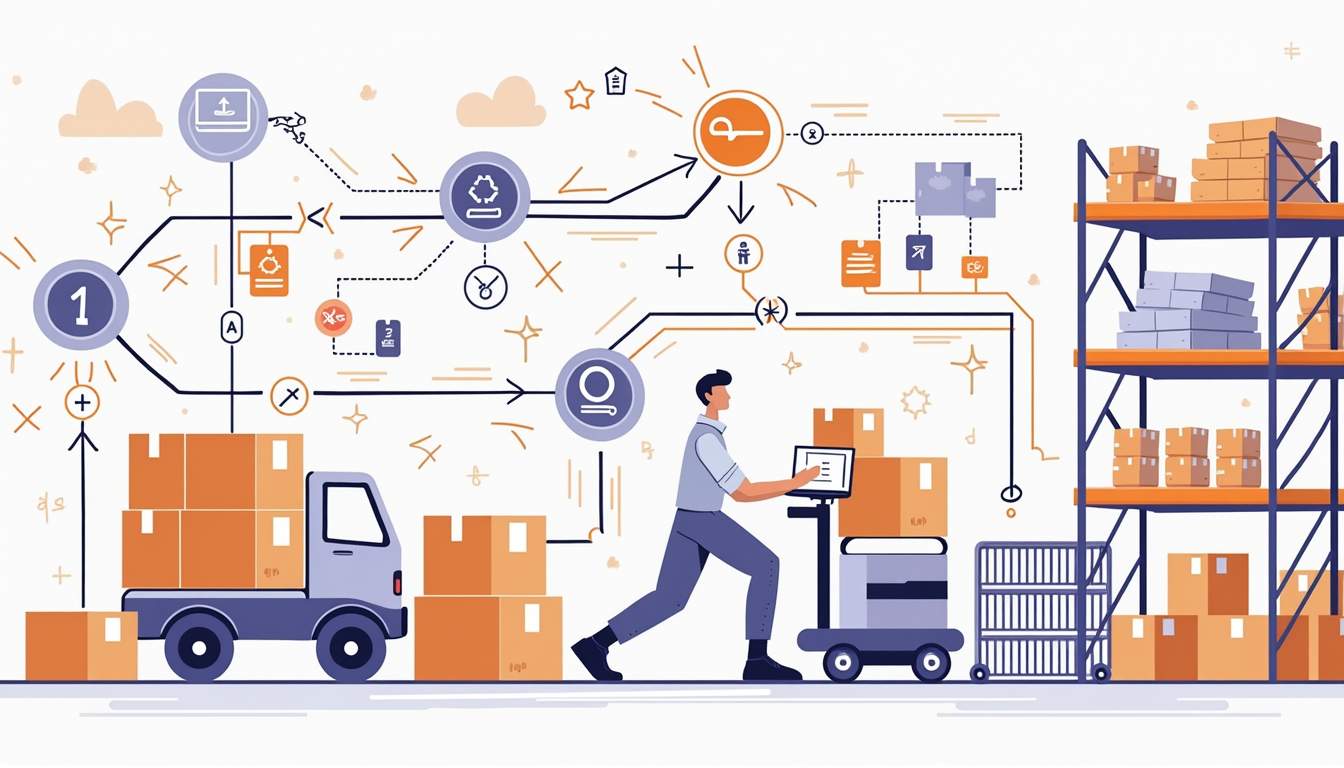
Next, organize the BOM in a logical and hierarchical structure, starting with the finished product and breaking it down into sub-assemblies and individual components. This structure should be easy to understand and navigate, facilitating communication and collaboration across teams.
Finally, ensure that the BOM is regularly updated and maintained. This involves tracking changes to product designs, specifications, and supplier information, and reflecting these changes in the BOM. Regular audits and reviews can help in identifying discrepancies and ensuring the accuracy and reliability of the BOM.
Integrating BOM with Inventory Management Systems
Integrating the BOM with inventory management systems can significantly enhance operational efficiency. This integration enables real-time synchronization of inventory data, ensuring that all stakeholders have access to the latest information. It also facilitates automation of inventory processes, such as reordering and stock adjustments, reducing manual effort and errors.
Moreover, integration with inventory management systems provides valuable insights into inventory performance and trends. By analyzing this data, businesses can identify opportunities for improvement and optimize their inventory strategies. This leads to better resource utilization, cost savings, and improved customer service.
Additionally, integration with other business systems, such as ERP and Customer Relationship Management (CRM) systems, can further enhance the benefits of a BOM. This holistic approach ensures seamless coordination and communication across all business functions, driving overall efficiency and effectiveness.
Challenges and Best Practices
Common Challenges in BOM Management
Managing a BOM can be challenging, especially for businesses with complex products and supply chains. One of the common challenges is maintaining the accuracy and consistency of the BOM. Errors and discrepancies can lead to production delays, quality issues, and increased costs.
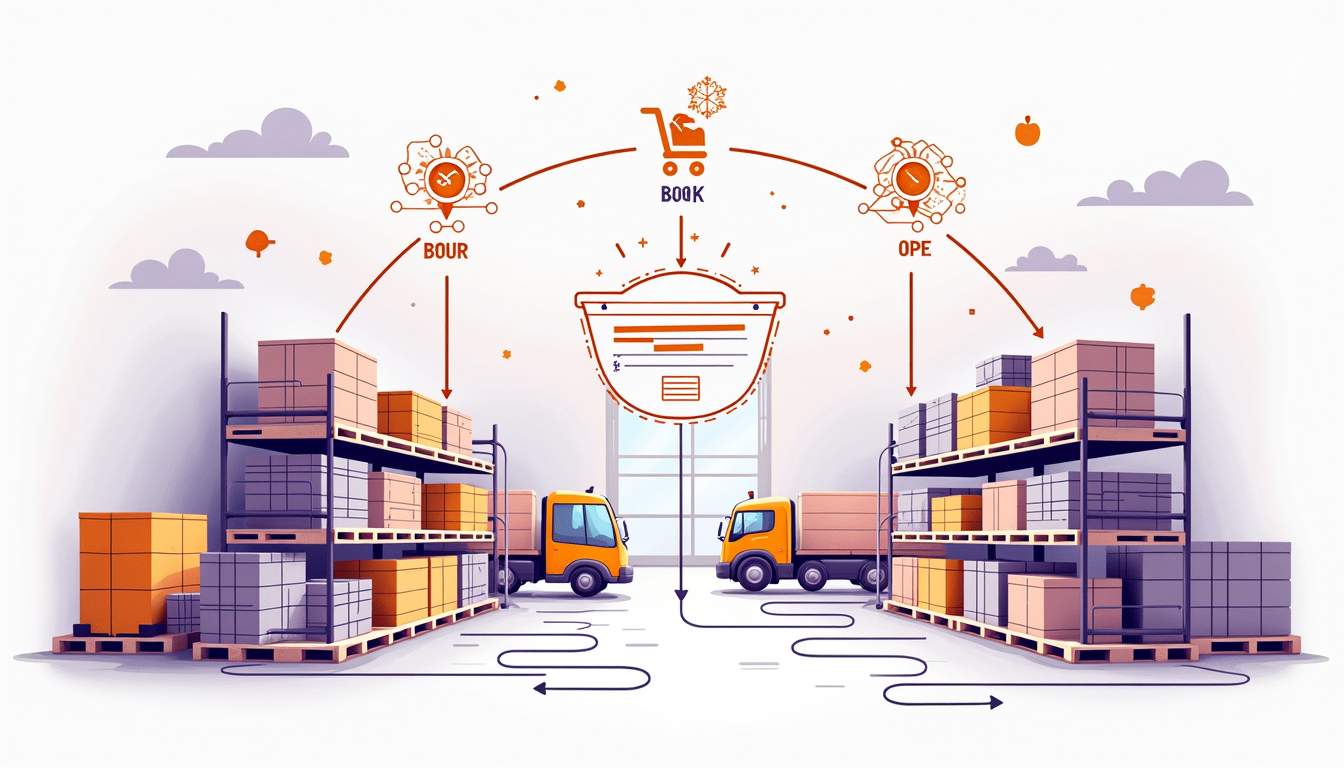
Another challenge is managing changes and updates to the BOM. As products evolve and new components are introduced, keeping the BOM up-to-date can be a daunting task. This requires effective change management processes and tools to track and document changes.
Additionally, integrating the BOM with other business systems can be complex and time-consuming. This requires careful planning and coordination to ensure seamless integration and data synchronization.
Best Practices for Effective BOM Management
To overcome these challenges, businesses should adopt best practices for effective BOM management. This includes establishing clear processes and guidelines for creating and maintaining the BOM, ensuring that all stakeholders are trained and informed.
Regular audits and reviews of the BOM can help in identifying and correcting errors and discrepancies. This ensures the accuracy and reliability of the BOM, reducing the risk of production issues and quality problems.
Leveraging technology and automation can also enhance BOM management. Tools such as Product Lifecycle Management (PLM) software can streamline BOM creation and maintenance, providing a centralized platform for collaboration and communication.
Conclusion
A Bill of Materials (BOM) is a critical tool for e-commerce businesses, enabling efficient inventory management and streamlined operations. By providing a detailed blueprint of product components and processes, a BOM enhances product quality, consistency, and supply chain management. Implementing a BOM requires careful planning and integration with other business systems, but the benefits far outweigh the challenges. By adopting best practices and leveraging technology, businesses can optimize their inventory strategies and achieve long-term success in the competitive e-commerce landscape.