The Importance of Safety Stock in Inventory Management: A Comprehensive Guide
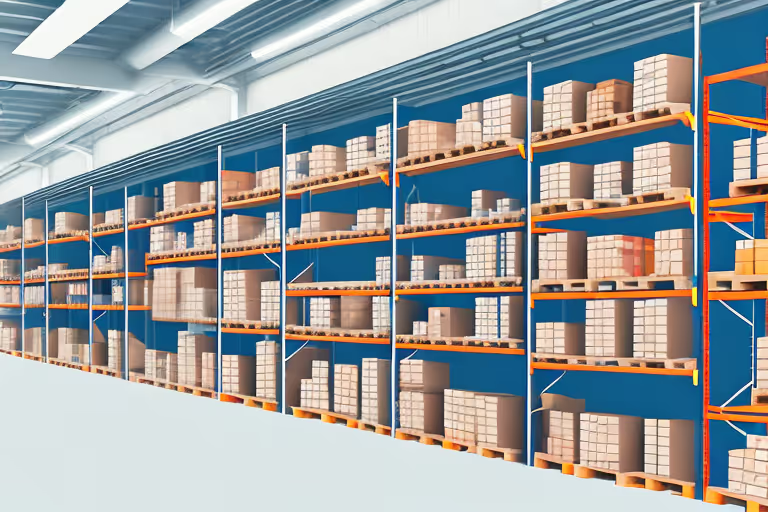
Inventory management is a critical aspect of any business that deals with the storage and sale of products. One key factor that plays a significant role in maintaining optimal inventory levels is safety stock. In this comprehensive guide, we will delve into the importance of safety stock, its various benefits, and strategies to calculate it effectively.
Understanding Safety Stock in Inventory Management
In inventory management, safety stock refers to the buffer inventory that is held in addition to the average inventory level to ensure uninterrupted supply and prevent stockouts. It acts as a cushion against unexpected fluctuations in demand, lead times, and forecast errors.
Safety stock is crucial for several reasons. Firstly, it acts as insurance against unforeseen shifts in customer demand. By having a buffer inventory, businesses can meet unexpected increases in customer orders without delays or stockouts, thus ensuring customer satisfaction and loyalty.
Secondly, safety stock plays a vital role in preventing stockouts, which can have severe consequences for businesses. Stockouts can result in lost sales, missed opportunities, and damage to a company's reputation. With safety stock in place, businesses can mitigate the risks associated with stockouts.
Stockouts can occur due to various factors such as sudden spikes in customer demand, supplier delays, or production disruptions. Safety stock acts as a buffer, allowing businesses to continue operations smoothly even during unforeseen circumstances. It provides a safety net against stockouts, ensuring that customers' needs are met consistently.
Lead time refers to the time taken from placing an order to receiving the products. Having safety stock can help businesses reduce lead times significantly. By holding a buffer inventory, businesses can fulfill customer orders immediately, even if there are delays in the replenishment process, thereby improving overall customer satisfaction.
Forecasting demand accurately is often challenging for businesses. However, safety stock can help compensate for demand forecasting errors. By maintaining extra inventory, businesses can ensure they have enough stock to satisfy customer demand, even if the actual demand deviates from the forecasted values.
Customer satisfaction is paramount for any successful business. Safety stock plays a pivotal role in meeting customer expectations by ensuring product availability and prompt order fulfillment. By having safety stock, businesses can provide a seamless customer experience and build long-term relationships.
Price fluctuations can significantly impact a business's profitability. Safety stock can act as a safeguard against these fluctuations. By procuring additional inventory when prices are low, businesses can protect themselves from sudden price increases and maintain profit margins without passing on price hikes to customers.
Overall, safety stock is an essential component of effective inventory management. It provides businesses with the flexibility and resilience to navigate through uncertain market conditions, meet customer demands, and maintain a competitive edge in the industry.
Calculating Optimal Safety Stock Levels Made Easy
Now that we understand the significance of safety stock, let's explore various methods to calculate optimal safety stock levels. Determining the right level of safety stock is crucial to ensure it effectively mitigates risks while also minimizing carrying costs.
One commonly used method to calculate optimal safety stock levels is the statistical approach. This approach involves analyzing historical demand data to identify patterns and trends. By using statistical techniques such as moving averages or exponential smoothing, businesses can forecast future demand and determine the amount of safety stock required to meet unexpected fluctuations.
Another method to calculate optimal safety stock levels is the lead time approach. Lead time refers to the time it takes for a business to receive inventory after placing an order. By analyzing historical lead time data, businesses can calculate the average lead time and determine the safety stock needed to cover any delays or uncertainties in the supply chain.
In addition to these methods, businesses can also consider the variability approach. This approach takes into account the variability in both demand and lead time. By calculating the standard deviation of demand and lead time data, businesses can determine the appropriate level of safety stock to account for any fluctuations or uncertainties in both factors.
Furthermore, businesses can utilize inventory optimization software to calculate optimal safety stock levels. These software solutions use advanced algorithms and data analysis techniques to analyze historical data, forecast demand, and determine the ideal safety stock level. By automating the calculation process, businesses can save time and ensure accuracy in their safety stock calculations.
It is important to note that calculating optimal safety stock levels is not a one-time task. As business conditions change, such as market demand, supplier reliability, or lead time variability, it is crucial to regularly review and adjust safety stock levels to maintain optimal inventory management.
In conclusion, calculating optimal safety stock levels is a critical aspect of effective inventory management. By utilizing various methods such as statistical analysis, lead time evaluation, variability consideration, and inventory optimization software, businesses can ensure they have the right amount of safety stock to mitigate risks and minimize carrying costs.
10 Methods to Calculate Safety Stock (with Formulas)
Using the Standard Deviation Formula for Safety Stock Calculation
The standard deviation formula calculates the variation in demand over a specified period. By analyzing historical demand data, businesses can quantify the standard deviation and estimate the safety stock required to cover unexpected demand fluctuations.
For example, let's consider a retail store that sells clothing. By analyzing the sales data for a specific product over the past year, the store can calculate the standard deviation of daily demand. This information can then be used to determine the safety stock needed to ensure that the store does not run out of inventory during periods of high demand.
In this case, the store might find that the standard deviation of daily demand for a particular clothing item is 20 units. To account for unexpected fluctuations in demand, the store may decide to keep a safety stock of 30 units. This means that even if demand exceeds the average daily sales by 20 units, the store will still have an additional 30 units on hand to fulfill customer orders.
Applying the Variable Demand Formula for Safety Stock Calculation
The variable demand formula takes into account the variability in customer demand. By determining the standard deviation of demand during lead time, businesses can calculate the safety stock needed to meet demand during that period.
Let's consider a manufacturing company that produces electronic devices. The company experiences fluctuations in customer demand due to seasonal trends and market conditions. To ensure that they can meet customer orders even during periods of high demand, the company uses the variable demand formula to calculate safety stock.
By analyzing historical data, the company determines that the standard deviation of demand during lead time is 50 units. Based on this information, they decide to keep a safety stock of 70 units. This ensures that even if demand exceeds the average during lead time by 50 units, the company will have an additional 70 units available to fulfill customer orders.
Utilizing the Variable Lead Time Formula for Safety Stock Calculation
Variable lead time refers to fluctuations in the time taken for suppliers to deliver products. By considering the variability in lead time, businesses can calculate safety stock that accounts for the potential extended lead times and ensures uninterrupted supply.
Let's consider a restaurant that relies on a supplier to deliver fresh produce. The supplier's lead time can vary due to factors such as weather conditions and transportation delays. To ensure that they always have enough fresh produce on hand, the restaurant uses the variable lead time formula to calculate safety stock.
By analyzing historical data, the restaurant determines that the standard deviation of lead time is 2 days. Based on this information, they decide to keep a safety stock of 3 days' worth of fresh produce. This means that even if the supplier's lead time exceeds the average by 2 days, the restaurant will still have an additional 3 days' worth of produce to maintain their menu offerings.
Determining Safety Stock with the EOQ Formula
The Economic Order Quantity (EOQ) formula calculates the optimal order quantity that minimizes total inventory costs. By incorporating safety stock into the EOQ formula, businesses can ensure adequate buffer inventory while optimizing order quantities and reducing costs.
Let's consider a wholesale distributor that supplies office supplies to businesses. The distributor wants to determine the optimal order quantity for a particular product to minimize inventory holding costs while ensuring that they can meet customer demand. They use the EOQ formula to calculate safety stock.
By analyzing historical demand data and considering factors such as order processing time and lead time, the distributor calculates the EOQ to be 500 units. To account for unexpected demand fluctuations, they decide to keep a safety stock of 100 units. This means that even if demand exceeds the average by a certain amount, the distributor will still have an additional 100 units on hand to fulfill customer orders.
Calculating Safety Stock with the Reorder Point Formula
The reorder point formula helps businesses determine the optimal inventory level at which a new order should be placed. By factoring in safety stock in the reorder point calculation, businesses can avoid stockouts and maintain continuous supply even during unexpected demand spikes or lead time fluctuations.
Let's consider an e-commerce retailer that sells consumer electronics. The retailer wants to ensure that they never run out of stock for a popular product. They use the reorder point formula to calculate safety stock.
By analyzing historical sales data, lead time, and considering factors such as customer demand patterns, the retailer determines that the reorder point for the product is 100 units. To account for unexpected demand spikes or lead time fluctuations, they decide to keep a safety stock of 50 units. This means that even if demand exceeds the average or lead time is longer than expected, the retailer will still have an additional 50 units available to fulfill customer orders.
Time-Based Safety Stock Calculation: A Practical Approach
A time-based approach to safety stock calculation involves setting a specific number of days' worth of inventory as safety stock. By analyzing historical demand patterns and lead times, businesses can identify the appropriate number of days that should be covered by safety stock.
Let's consider a grocery store that wants to ensure that they always have enough stock of essential items such as milk and bread. The store uses a time-based approach to calculate safety stock.
By analyzing historical sales data and lead times, the store determines that on average, it takes 2 days for a new order to arrive. To ensure uninterrupted supply, they decide to keep a safety stock of 3 days' worth of inventory for essential items. This means that even if demand exceeds the average or lead time is longer than expected, the store will still have an additional 3 days' worth of inventory to meet customer needs.
Understanding Fixed Safety Stock and Its Calculation
Fixed safety stock refers to a predetermined quantity of additional inventory that is kept as a buffer. It acts as a constant safeguard against uncertainties in demand or lead time. The calculation of fixed safety stock typically involves a combination of historical data, safety stock ratios, and qualitative assessments.
Let's consider a manufacturing company that produces automotive parts. The company wants to ensure that they always have enough inventory to meet customer demand, even during unexpected disruptions in the supply chain. They use a fixed safety stock approach to calculate safety stock.
By analyzing historical data, considering safety stock ratios recommended for their industry, and conducting qualitative assessments, the company determines that a fixed safety stock of 200 units is appropriate for their operations. This means that regardless of demand fluctuations or lead time variations, the company will always have an additional 200 units of inventory as a buffer.
By understanding the importance of safety stock in inventory management and implementing effective strategies to calculate optimal safety stock levels, businesses can optimize their inventory management, reduce stockouts, and enhance customer satisfaction. Remember, safety stock serves as a valuable tool in managing uncertainties and maintaining a competitive edge in today's dynamic business environment.