Mastering Inventory Replenishment: A Comprehensive Guide
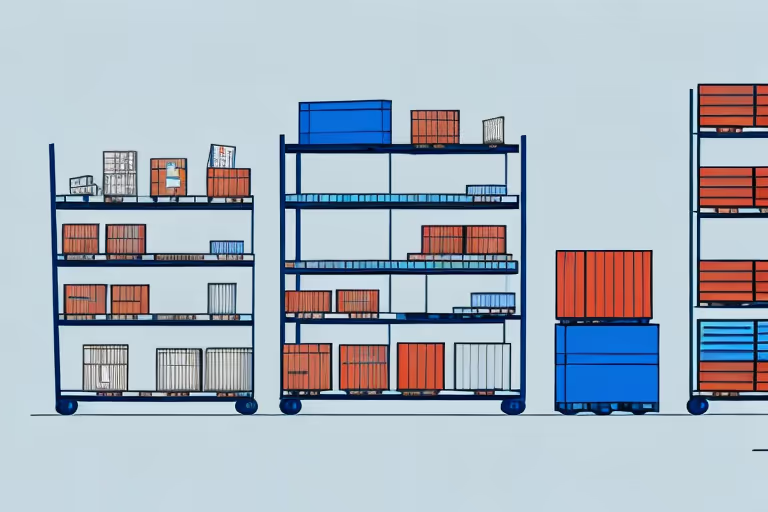
Inventory replenishment is a crucial aspect of efficient supply chain management. It involves restocking products at the right time and in the right quantity to meet customer demand and ensure smooth operations. In this comprehensive guide, we will explore the key principles and best practices for mastering inventory replenishment.
Understanding Inventory Replenishment
Inventory replenishment is a vital aspect of managing stock for any business. It involves the regular restocking of products to ensure that they are available when customers need them. By implementing effective inventory replenishment strategies, businesses can avoid stockouts, maintain optimal stock levels, and provide a smooth operation for their customers.
The Importance of Stock Replenishment
Keeping a well-maintained stock is crucial for the success of any business. Inventory replenishment plays a critical role in ensuring that products are readily available to meet customer demand. It helps businesses avoid stockouts, which can lead to customer dissatisfaction and lost sales. By replenishing stock regularly, companies can maintain a consistent supply of products, improving customer satisfaction and overall profitability.
Avoiding Stockouts: A Key Benefit of Inventory Replenishment
Stockouts can have a detrimental impact on a business. Not only do they result in dissatisfied customers, but they also affect the overall profitability. Implementing effective inventory replenishment strategies helps businesses minimize the risk of stockouts. By continuously monitoring stock levels and replenishing inventory in a timely manner, companies can ensure that products are always available to meet customer demand.
Furthermore, avoiding stockouts also helps businesses maintain a positive reputation. When customers can rely on a company to consistently have the products they need in stock, it builds trust and loyalty, encouraging repeat purchases and positive word-of-mouth recommendations.
Balancing Inventory: Preventing Overstocking
While avoiding stockouts is crucial, overstocking can also pose challenges for businesses. Maintaining excessive inventory ties up capital, occupies valuable warehouse space, and can lead to increased holding costs. Therefore, finding the right balance is key.
Inventory replenishment plays a significant role in achieving optimal stock levels. By analyzing sales data, monitoring market trends, and forecasting demand, businesses can replenish inventory in a way that avoids overstocking. This ensures that they have enough stock to meet customer demand without tying up excessive resources.
Managing Safety Stock for a Smooth Operation
Safety stock is an essential component of inventory replenishment. It acts as a buffer to protect against unexpected fluctuations in demand or supply chain disruptions. Maintaining an appropriate level of safety stock is crucial for a smooth operation.
Inventory replenishment ensures that the safety stock is consistently maintained. By regularly monitoring stock levels and adjusting replenishment orders based on demand and market conditions, businesses can effectively manage potential disruptions. This allows for a smooth operation, even during uncertain times, and minimizes the impact of unexpected events on customer satisfaction and overall business performance.
Keeping Customers Happy with Efficient Replenishment
Efficient replenishment processes directly impact customer satisfaction. When products are readily available, customers experience faster order fulfillment, shorter lead times, and reliable delivery. This contributes to building trust and loyalty, enhancing the overall customer experience.
Inventory replenishment plays a crucial role in ensuring efficient order fulfillment. By streamlining the replenishment process, businesses can optimize their stock levels, reduce the time it takes to fulfill orders, and improve overall operational efficiency. This not only benefits customers but also allows businesses to maximize their revenue potential and maintain a competitive edge in the market.
Cost Savings: Lowering Shipping Costs through Inventory Replenishment
Inventory replenishment offers cost-saving opportunities for businesses, particularly in terms of shipping costs. By consolidating orders and replenishing stock in larger quantities, companies can take advantage of volume discounts offered by shipping carriers.
Consolidating orders allows businesses to reduce the number of shipments, leading to lower freight expenses. Additionally, by replenishing stock in larger quantities, companies can optimize their shipping processes, further reducing costs and improving overall cost efficiency.
Inventory replenishment not only ensures that products are available for customers but also helps businesses save money on shipping expenses, contributing to improved profitability and financial performance.
Exploring Different Inventory Replenishment Methods
Inventory replenishment is a crucial aspect of managing a successful business. Finding the right method to replenish inventory can significantly impact a company's profitability and customer satisfaction. In this article, we will delve into four different inventory replenishment methods, each with its unique advantages and considerations.
Reorder Point Method: A Reliable Approach to Replenishment
The reorder point method is a widely used approach to inventory replenishment. It relies on setting a predetermined stock level at which it triggers the replenishment process. By calculating the reorder point based on historical data and lead times, businesses can maintain inventory levels that meet demand without risking stockouts.
One of the key benefits of the reorder point method is its reliability. By considering historical data, businesses can anticipate demand patterns and adjust their inventory levels accordingly. This method ensures that businesses always have enough stock on hand to fulfill customer orders, avoiding lost sales opportunities.
Another advantage of the reorder point method is its simplicity. Once a business determines its reorder point, it becomes a straightforward process of monitoring inventory levels and initiating replenishment when the stock reaches that point. This simplicity makes it an attractive option for businesses of all sizes and industries.
Top-Off Replenishment Method: Optimizing Inventory Levels
The top-off replenishment method takes a proactive approach to inventory management. It involves regularly reviewing inventory levels and topping them off to predefined levels. This approach ensures that inventory remains at optimal levels, avoiding stockouts while minimizing overstocking.
One of the main advantages of the top-off replenishment method is its ability to optimize inventory levels. By regularly reviewing inventory and replenishing to predefined levels, businesses can strike a balance between meeting demand and minimizing carrying costs. This method is particularly useful for products with stable demand patterns.
Additionally, the top-off replenishment method allows businesses to take advantage of economies of scale. By replenishing inventory in larger quantities, businesses can negotiate better pricing and reduce overall procurement costs. This approach can contribute to improved profitability and a competitive edge in the market.
Periodic Replenishment Method: Finding the Right Timing
The periodic replenishment method involves restocking inventory at specific time intervals. This method is based on analyzing demand patterns and sales data to determine the ideal replenishment frequency. By replenishing inventory at the right timing, businesses can avoid stockouts and optimize inventory levels.
One of the key advantages of the periodic replenishment method is its flexibility. Businesses can tailor the replenishment frequency based on their specific needs and industry dynamics. For products with fluctuating demand, a more frequent replenishment schedule may be necessary, while for products with stable demand, a less frequent schedule may suffice.
Implementing the periodic replenishment method requires careful analysis of demand patterns and sales data. Businesses need to identify trends and seasonality factors that can impact inventory levels. By having a deep understanding of these factors, businesses can fine-tune their replenishment strategy and ensure optimal inventory levels at all times.
On-Demand Replenishment Method: Meeting Immediate Needs
In certain industries or situations, immediate replenishment is necessary to meet sudden spikes in demand or unforeseen circumstances. The on-demand replenishment method allows businesses to react quickly and ensure availability during critical times.
The on-demand replenishment method is particularly relevant for industries with unpredictable demand patterns or industries that deal with perishable goods. For example, in the food industry, where freshness is crucial, the ability to replenish inventory on-demand can make a significant difference in customer satisfaction and product quality.
Implementing the on-demand replenishment method requires strong supplier relationships and efficient logistics capabilities. Businesses need to have reliable suppliers who can deliver inventory quickly, and they must have efficient processes in place to handle urgent orders. By investing in these areas, businesses can meet immediate needs and maintain a competitive edge in the market.
As we have explored, there are various inventory replenishment methods available to businesses. Each method has its own advantages and considerations, and the choice of method depends on factors such as industry dynamics, demand patterns, and the nature of the products or services offered. By carefully evaluating these factors and choosing the most suitable replenishment method, businesses can effectively manage their inventory levels, meet customer demands, and drive overall success.
Implementing Best Practices for Effective Inventory Replenishment
Inventory replenishment is a critical aspect of managing a successful business. It involves ensuring that the right products are available at the right time and in the right quantities. To achieve this, businesses need to implement best practices that optimize their inventory management processes. In this article, we will explore three key practices that can enhance inventory replenishment efficiency.
1. Fine-Tuning Demand Forecasts for Accurate Replenishment
Accurate demand forecasting is the foundation of effective inventory replenishment. By analyzing historical sales data, market trends, and customer behavior, businesses can improve their forecasting accuracy. This data-driven approach allows companies to make informed decisions regarding when and how much inventory needs to be replenished.
However, demand forecasting is not a one-time task. It requires continuous monitoring and adjustment to account for changing market conditions and customer preferences. By regularly reviewing and fine-tuning their demand forecasts, businesses can ensure that their inventory replenishment efforts align with actual demand, minimizing the risk of overstocking or stockouts.
2. Enhancing Collaboration for Seamless Replenishment
Inventory replenishment involves multiple stakeholders and departments within a company. To ensure seamless coordination and alignment across the supply chain, businesses need to foster collaboration and open communication.
By establishing cross-functional teams and regular meetings, businesses can bring together representatives from sales, operations, procurement, and logistics. This collaborative approach allows different departments to share relevant information, such as sales forecasts, production schedules, and supplier lead times. With this shared knowledge, businesses can make more accurate replenishment decisions and avoid misalignment between demand and supply.
Furthermore, collaboration with external partners, such as suppliers and distributors, is also crucial. By establishing strong relationships and sharing real-time data, businesses can improve visibility into the supply chain and respond quickly to changes in demand or supply disruptions.
3. Real-Time Inventory Monitoring for Timely Replenishment
Real-time inventory monitoring is a game-changer for effective replenishment. By leveraging technology and automated systems, businesses can track stock levels, identify potential discrepancies, and proactively initiate replenishment actions.
Advanced inventory management software and sensors enable businesses to have real-time visibility into their inventory across multiple locations. This visibility allows them to identify low stock levels or unexpected spikes in demand and take immediate action to replenish inventory. By reducing the time lag between demand signals and replenishment actions, businesses can minimize the risk of stockouts and ensure uninterrupted operations.
Moreover, real-time inventory monitoring also helps businesses identify inefficiencies in their replenishment processes. By analyzing data on stock turnover, order lead times, and supplier performance, companies can identify bottlenecks and implement process improvements to optimize their inventory management.
Mastering inventory replenishment requires a holistic approach that encompasses understanding its importance, exploring different replenishment methods, and implementing best practices. By continuously evaluating and fine-tuning these strategies, businesses can optimize inventory levels, minimize stockouts, and keep customers satisfied. With efficient inventory replenishment, businesses can thrive in today's competitive marketplace.